Magnetic Force Microscopy (MFM)
Magnetic Force Microscopy (MFM)
The method magnetic force microscopy or MFM described here is the main method of scanning probe microscopy to probe samples with magnetic properties or magnetic materials and elucidate features such as magnetic domains and domain walls in a sample. This method is widely used in the field of magnetic storage media for quality control.
In MFM, the magnetic forces acting on a sharp, magnetized tip by the sample are measured. During this measurement the tip is lifted off the surface in order to separate the long-range magnetic forces from the short-range atomic forces between tip and sample. Magnetic force microscopy operates in amplitude modulation mode, a type of dynamic force mode where a cantilever with a thin magnetic coating is driven at its resonance frequency, typically in the tens or hundreds of kilohertz (this mode is also referred to as tapping mode). These cantilevers are inexpensive and commercially available. MFM maps the phase and frequency of the oscillating cantilever as it passes over at a prescribed height over the sample. A repulsive magnetic force gradient will cause the resonance curve to shift to a higher frequency, accompanied by an increase in phase shift (bright contrast). Conversely, an attractive magnetic force gradient results in the resonance curve shifting to a lower frequency, accompanied by a decrease in phase shift (dark contrast). The advantages of MFM operation in dynamic mode are lower noise and higher resolution. The tip-sample distance is a crucial parameter to optimize for effective MFM operation. If the tip is too far from the sample, the resolution will be compromised. If the tip is too close to the sample, the topography will be convoluted into the MFM signal, significantly complicating its interpretation.
MFM can operate in either a single or dual pass technique. In the single-pass setup, the MFM tip passes over the sample at a constant height. An advantage of the single pass mode is that the tip is closer to the sample so there is higher sensitivity and resolution in the magnetic force measurement, but the spatial resolution may suffer. This implementation of MFM is the fastest, minimizes tip wear, and has a more straightforward theoretical interpretation.
In the dual pass setup, the cantilever passes twice over every line in the image. During the first pass, the MFM tip is in contact with the sample as it maps out the topography in amplitude modulation mode. The tip is then lifted over the sample surface for the second pass by an amount prescribed by the user. In the second pass, the tip follows the contours of the topography but now at a distance above the sample. The tip-sample distance is optimized during every image and is typically a few or tens of nanometers. Optimization entails a tradeoff between having the tip as close to the sample as possible but not being too close as to crash into the sample.
Examples of magnetic force microscopy
Below are MFM images of polished stainless steel. On the left is an 80µm x 80µm topography image showing a very smooth surface with some polishing marks running diagonally across the surface. The middle image is the corresponding MFM phase image for this area, revealing very distinct features and morphology not evident in the topography image. The MFM clearly shows magnetic domains and the magnetic ferrite phase in the maze-like pattern. On the far right is a 13µm x 13µm zoom-in of the magnetic ferrite phase image.
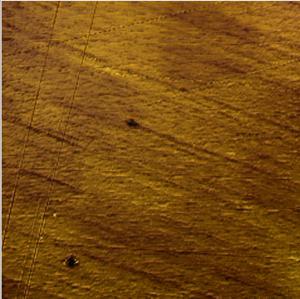
Topography of a polished stainless steel sample. Scan size: 80 µm. Height range: 50 nm.
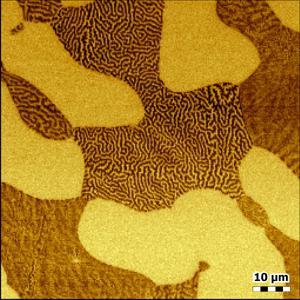
Magnetic force microscopy (MFM) of the same 80 µm × 80 µm area. Phase range: 10°.
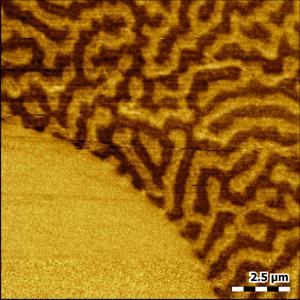
Magnetic force microscopy (MFM) of a smaller area. Scan size: 13 µm. Height range: 50 nm.
Below is an example of an MFM measurements of a samples in the data storage industry, where MFM is critical to studying material and property defects. The two images show the topography and corresponding MFM phase image of a hard disk drive platter. The topography clearly shows the recording tracks. The MFM image shows dark and bright areas, corresponding to magnetization reversal where white stands for repulsive forces and black for attractive forces.
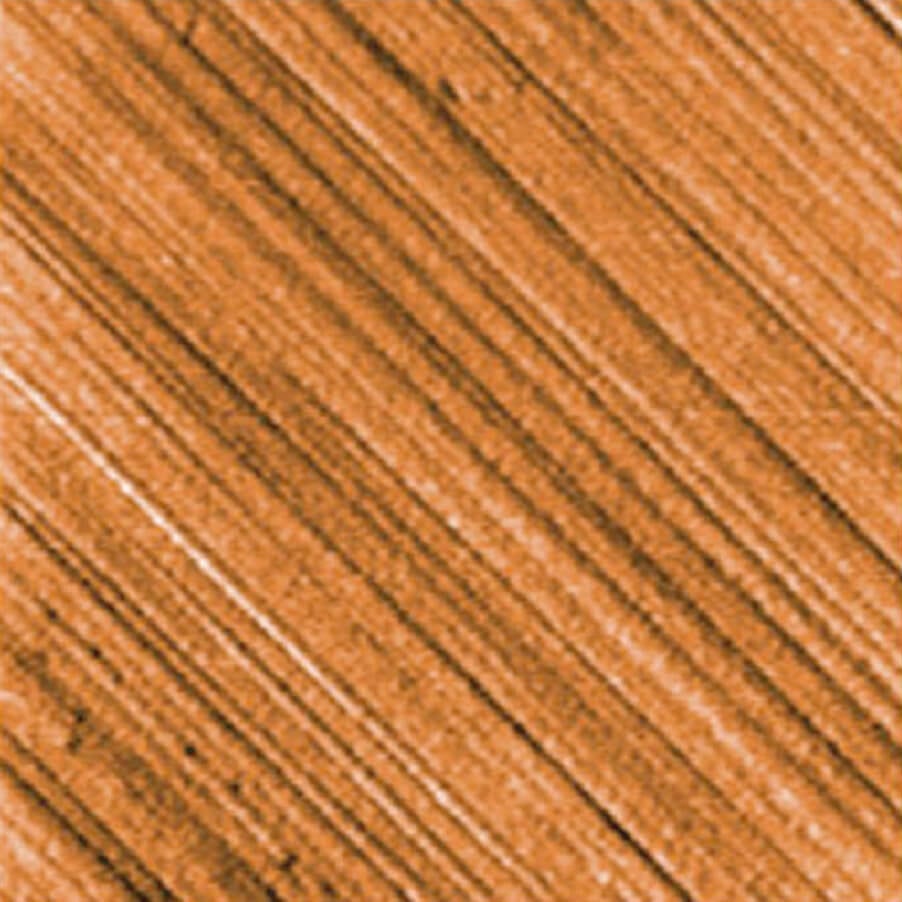
Surface topography measurement (dynamic force mode) of a hard disk drive platter. The recording tracks, as evident in the MFM image, run parallel to the grooves. Scan range: 2 µm. Height range: 5 nm.
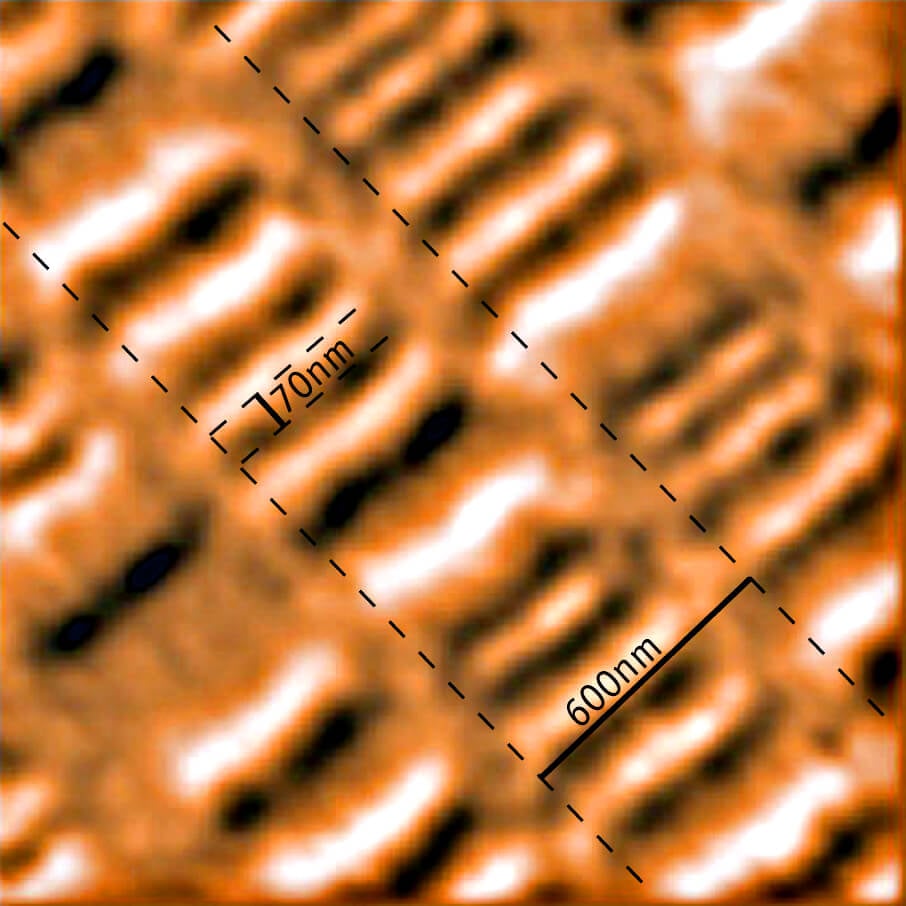
Magnetic force microscopy (MFM) measurement of a hard disk drive platter (same area). White and black areas show magnetization reversal, where white stands for repulsive forces and black for attractive forces. Scan range: 2 µm. Phase range: 5°.
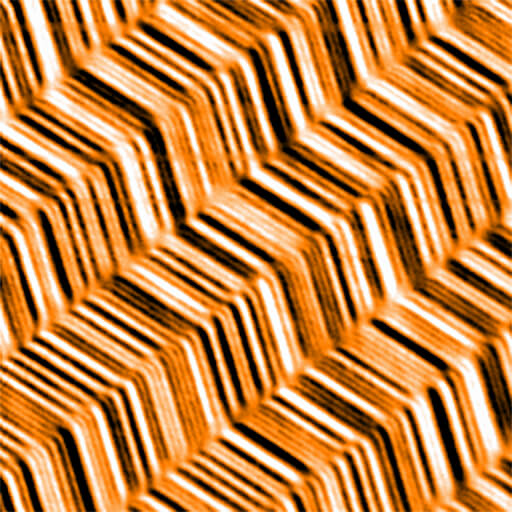
Magnetic force microscopy (MFM) of digital backup tape with magnetically stored data. Scan size: 50 µm.