Discover how Atomic Force Microscopy (AFM) is revolutionizing industries by providing unparalleled insights into ...
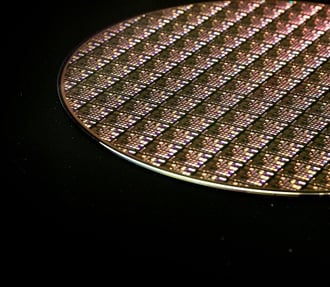
22.10.2024
The ultimate tool for nanoscale research from biological molecules to advanced new materials.
The versatile mid-range research AFM that grows with your demands in modes and accessories.
A compact affordable research AFM that is astoundingly easy to use, with more than 30 modes and options.
Measure roughness and other material properties of heavy and large samples up to 300 mm and 45 kg.
Bringing the power of DriveAFM to a wafer metrology system purpose-built for the requirements of the semiconductor industry.
For unique requirements, we will design a bespoke AFM solution, leveraging our decades of engineering expertise.
Slide an AFM onto your upright optical microscope turret for a leap in resolution.
One of the smallest ever AFMs, created for integration into custom stages or existing setups.
A flexibly mountable research-grade scan head for integration into custom stages or existing set ups.
What is atomic force microscopy (AFM)? How does AFM work? What AFM modes do I really need? How do I get started with AFM?
Learn how AFM works with cantilever/tip assembly interacting with the sample. Explore CleanDrive technology, calibration methods, and feedback principles for precise nanoscale imaging.
An overview of common AFM modes. To learn about each mode in more detail and see application, view the full article.
We regularly publish detailed reviews providing practical guidance and theoretical background on various AFM applications.
Read detailed technical descriptions about selected AFM techniques and learn how to perform specific measurements on Nanosurf instruments.
A library of links to research papers in which Nanosurf instruments were used.
Learn AFM from our library of recorded webinars, covering different measurement techniques, modes, and areas of application.
Short video clips explaining how to perform different operations on Nanosurf instruments.
Watch a product demonstration to learn about the capabilities of our AFMs.
Short videos of our AFMs.
Browse news articles, press releases and a variety of other articles all around Nanosurf.
Browse Héctor Corte-Léon's weekly experiments, for inspiration, entertainment, and to discover everyday applications of AFM.
How can we determine which parameters to use for measuring elasticity?
When it comes to measuring the elasticity of materials using force spectroscopy, selecting the right parameters is crucial. In this post we will delve into the factors that influence the choice of parameters and discuss how optimizing them can lead to more accurate and insightful measurements. By understanding the impact of variables such as cantilever spring constant, force curve length, baseline definition, and approach/retraction speed, we can improve the reliability of elasticity measurements and gain a deeper understanding of material properties.
Cantilever Spring Constant and Material Matching
The choice of an appropriate cantilever is the first step in determining elasticity. The spring constant of the cantilever should be carefully selected to match the material being probed. Using a cantilever that is excessively stiff or too soft can lead to inaccurate results. A mismatched cantilever may not provide the desired sensitivity affecting the measured elasticity. Therefore, understanding the mechanical properties of the material and selecting a compatible cantilever is crucial.
Influence of Force Curve Length and Baseline Definition
The length of the force curve that is used to probe the sample plays a significant role in elasticity measurements. A force distance curve contains several distinct regions that are passed throughout an indentation experiment, which is schematically depicted in the figure below. Initially, the cantilever is far away from the surface and upon moving closer to the surface, the force acting on the cantilever virtually does not change. Very close to the surface, the cantilever might be pulled into contact with the surface, the so-called snap-in. As the piezo keeps extending, the cantilever deflects and thus exerts a force onto the surface below. After reaching a pre-defined force threshold, the piezo inverts the direction of its movement and the force applied to the surface is again reduced. If the cantilever tip adheres to the surface upon retraction, this causes a bending of the cantilever towards the surface, thus applying a pulling force on the interaction between tip and surface. Once this interaction is broken (adhesion event), the cantilever returns to its resting position.
This cycle is defined by three characteristics. First, the baseline, which is the region where the cantilever is not in contact with the surface and in its resting position. Second, the contact region, where the cantilever applies a force to the surface. And third, the adhesion region, where a pulling force is applied to the surface-tip interaction.
Accurate baseline definition is essential for reliable elasticity measurements, because it serves as the zero force reference for the forces applied to the surface. For example, if the length of the force curve is too short, the baseline region may not be well defined, or the cantilever may not even come out of contact with the surface at the end of the retract motion. The latter might be the case for e.g. soft material that can be easily indented. To choose the correct force curve length, one must take into account both the possible indentation depth and a sufficient baseline length.
Considerations for Approach and Retraction Speed
The speed at which the cantilever approaches and retracts from the sample is another critical parameter in force spectroscopy. The choice of speed depends on the material's viscoelastic properties and the specific goals of the experiment. For viscoelastic materials, the speed of approach and retraction can affect the measured elasticity. At higher speeds visco-elastic materials tend to appear stiffer or show a higher Young’s modulus as viscous effects kick in. However, excessively slow speeds may lead to experimental artifacts or prolonged measurement times.
In comparative measurements, where multiple samples or regions are analyzed, maintaining a constant ramp speed is advisable. This approach ensures consistency and allows for accurate comparisons between different regions or samples.
Conclusion
Optimizing parameters in force spectroscopy is essential for obtaining accurate and meaningful measurements of material elasticity. By carefully selecting a cantilever with an appropriate spring constant, determining the suitable force curve length and baseline definition, and considering the approach and retraction speed, we can enhance the reliability and accuracy of elasticity measurements. These optimizations lead to valuable insights into the mechanical properties of materials, enabling researchers to make informed decisions and advance their understanding in various scientific and engineering fields.
By following these guidelines, researchers can maximize the potential of force spectroscopy in studying elasticity and its correlation with other material properties. Understanding how parameters influence measurements empowers scientists to extract more precise data and to contribute to the ongoing exploration of material behavior.
Can nanoindentation be performed using AFM? Or is there a way to determine if the laser position is optimal and will not result in a wavy baseline?
Find the answers to these and other questions in our frequently asked questions document:
22.10.2024
Discover how Atomic Force Microscopy (AFM) is revolutionizing industries by providing unparalleled insights into ...
09.09.2024
Explore the strengths and limitations of Atomic Force Microscopy (AFM), Scanning Electron Microscopy (SEM), and ...
29.11.2023
Discover how Nanosurf's collaboration with a team of scientists has revolutionized spring constant calibration for ...
11.07.2024
FridayAFM: learn how to perform datamining on large sets of AFM data.
02.07.2024
FridayAFM: learn how to automatize data analysis in MountainsSPIP
26.06.2024
FridayAFM: learn how AFM makes possible modern ball point pens.
Interested in learning more? If you have any questions, please reach out to us, and speak to an AFM expert.