Students from Kirschgarten Gymnasium explore AFM technology at Nanosurf, gaining practical insights into nanotechnology ...
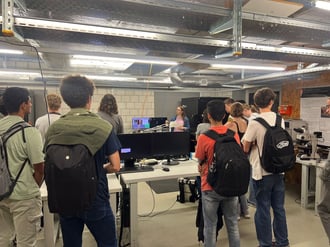
12.06.2024
The ultimate tool for nanoscale research from biological molecules to advanced new materials.
The versatile mid-range research AFM that grows with your demands in modes and accessories.
A compact affordable research AFM that is astoundingly easy to use, with more than 30 modes and options.
Measure roughness and other material properties of heavy and large samples up to 300 mm and 45 kg.
Bringing the power of DriveAFM to a wafer metrology system purpose-built for the requirements of the semiconductor industry.
For unique requirements, we will design a bespoke AFM solution, leveraging our decades of engineering expertise.
Slide an AFM onto your upright optical microscope turret for a leap in resolution.
One of the smallest ever AFMs, created for integration into custom stages or existing setups.
A flexibly mountable research-grade scan head for integration into custom stages or existing set ups.
What is atomic force microscopy (AFM)? How does AFM work? What AFM modes do I really need? How do I get started with AFM?
Learn how AFM works with cantilever/tip assembly interacting with the sample. Explore CleanDrive technology, calibration methods, and feedback principles for precise nanoscale imaging.
An overview of common AFM modes. To learn about each mode in more detail and see application, view the full article.
We regularly publish detailed reviews providing practical guidance and theoretical background on various AFM applications.
Read detailed technical descriptions about selected AFM techniques and learn how to perform specific measurements on Nanosurf instruments.
A library of links to research papers in which Nanosurf instruments were used.
Learn AFM from our library of recorded webinars, covering different measurement techniques, modes, and areas of application.
Short video clips explaining how to perform different operations on Nanosurf instruments.
Watch a product demonstration to learn about the capabilities of our AFMs.
Short videos of our AFMs.
Browse news articles, press releases and a variety of other articles all around Nanosurf.
Browse Héctor Corte-Léon's weekly experiments, for inspiration, entertainment, and to discover everyday applications of AFM.
Héctor here, your AFM expert at Nanosurf calling out for people to share their Friday afternoon experiments. Today I put the mechanical properties of the nettle plant stinging hairs to the test.
I grew up in the countryside, and one of the first things my sister and I learnt is to stay away from nettle plants (Urtica dioica). A brief touch and that's it, it is going to itch for half an hour at least. This is why while I explored the other things around me to see the details, the nettle plants were a big unknown to me (same for snakes, but better not to touch that topic...).
So, this week I bought a nice nettle plant (with stinging hairs, but not the Urtica dioica), the Coleus or painted nettle.
My original idea was too ambitious (yet I still think is possible, I just need more tries). Let me explain.
Our DriveAFM system has a readout laser for detecting cantilever movement, and a photothermal excitation laser to heat up the cantilever and produce movement. One of the beauties of this way of exciting cantilevers is that AFM probes don't need to necessarily be mounted on the AFM for the lasers to operate. This means that we can do things such as those shown in the next figure.
I mounted a probe onto the AFM (Multi-75E), and put another probe on top of the sample stage, mounted onto a detached probe holder (the probe, Tap-150 is mounted upside down in respect to the detached probe holder so it's reflective side is facing the AFM).
Using the approaching motors and the automated stage, I brought the two cantilevers in close proximity, and once they were there, I used the lasers to characterize them. First I performed a thermal tune on the Multi-75E, showing its resonant peak at about 73 kHz (and a minor peak at about 470 kHz), then, using the lasers motors, to position the lasers over the Tap-150, I repeated the thermal tune and found the resonant peak of the probe at about 158 kHz. You can see the whole process in video once more here:
Once I characterized both probes independently, I brought them close together to see what happens to the whole system once they are "coupled".
1 Using the readout and photothermal excitation lasers to characterize two probes pressing against each other, one that is mounted onto the AFM (Multi-75E) and one that is lying on the sample holder (Tap-150).
This time I used the photothermal laser and sweep its frequency to see at which frequency I find resonant peaks. First I repeat the Multi-75E on its own, finding the same peak I found with the thermal tune. Then, I pushed one probe against the other (we see this by monitoring the photodiode and noticing that when the two probes are coupled together, there is some deflection on the Multi-75E probe). Then I performed the same frequency sweep and I found that this time we don't see the 73 kHz but one at 142 kHz.
I went even further, and excited the Tap-150 instead while keeping the readout laser on the Multi-75:
I lack sufficient knowledge to interpret these results properly, but it seems that for this case, when we monitor the soft probe with low resonant frequency, we see (almost unaltered) the mechanical properties of the stiffer probe. Can this be applied to gain knowledge about other systems? Can we obtain some knowledge about the nettle plant stings? As we can see in the next figure, the stings are really tiny and look flimsy enough for an AFM probe to be able to move them without breaking. So I cut a branch from the painted nettle plant and mounted it in the sample holder. I used the clips to hold it in place and a gold coated glass slide to provide some contrast.
It took great care to bring the Multi-75E probe close to one of the stings, but with the help of the approach motors and the automated stage (both allowing to move only a few micrometers at a time when needed), eventually I managed to bring things together.
Once they are close together, by monitoring the deflection it is possible to determine when they are in "contact", although, in this occasion I was not measuring the force (which could be a very interesting experiment).
As before with the Tap-150, I performed a frequency sweep, interestingly, I found three peaks. Probably the one at about 62 kHz is the original peak from the Multi-75E probe and the other two belong to the sting, one at about 95 kHz and another at a much lower frequency, about 37 kHz. At this point, there isn't much more we can do without a numerical model of the sting structure, however, hopefully, somebody with the capability to do the modelling part will take this as inspiration and continue where I left off.
However, there is something else we can do apart from mechanical properties. We can image the surface of the sting and map the nanomechanical properties.
The surface of the sting is dotted with protuberances. According to literature, this could be a trick to reinforce the structure without having to add a lot of mass to the system, or to modify the hydrophobicity, or to create and antibacterial effect. It is interesting to note from the elastic modulus map that the protuberances have different stiffness than the rest of the surface. However, by looking at the adhesion it's possible to see that there are areas covered in some residue (water? wax?), and this modifies the behaviour of the stiffness map. In the areas exposed, the stiffness of the surface is closer to that of the protuberances (which are exposed), while in the areas where the surface is not exposed, the stiffness is much more different than that of the protuberances. Probably the best is to compare both in the case where they are exposed, but I don't know if the layer penetrates underneath and affects the plant tissue underneath in addition to adding a soft layer on the surface.
So, what was my initial plan? To take a sting with tweezers, clamp it onto the probe holder and use it to image. It will be less sharp than an AFM probe, but it will an interesting experience. Or at least, glue it somehow to the cantilever and use the end of the sting instead of the probe apex. I didn't managed, but I still think it can be done and quite interesting.
I hope you enjoyed what I showed you, that it brings you new ideas to experiment yourselves, and that this information about the painted nettle plant is useful to somebody.
Stay in touch, and if you have more info, please share.
... and if you made it this far, here are some discarded images. Exciting the sting with the laser (see how the peak at high frequency increases its amplitude), and probing a probe resting on a gel-pack box (a ContGD probe).
12.06.2024
Students from Kirschgarten Gymnasium explore AFM technology at Nanosurf, gaining practical insights into nanotechnology ...
29.11.2023
Discover how Nanosurf's collaboration with a team of scientists has revolutionized spring constant calibration for ...
16.10.2023
Discover how Dr. Nitya Nand Gosvami and his team at IIT Delhi harnessed the power of Nanosurf's FlexAFM and DriveAFM ...
08.12.2024
Learn how to make a Python code to interface your AFM with a gamepad.
01.10.2024
FridayAFM: learn how the extreme sensitivity of AFM can reveal the glass ageing process.
11.07.2024
FridayAFM: learn how to perform datamining on large sets of AFM data.
Interested in learning more? If you have any questions, please reach out to us, and speak to an AFM expert.